Have you ever wondered why selecting the right cutter pitch matters in machining? In today's competitive manufacturing landscape, precision and efficiency are paramount. The choice of cutter pitch can significantly influence productivity, stability, and overall machining performance. This is not just about optimizing tools but ensuring that every operation aligns with the highest standards of quality and speed.
Tungaloy Corporation, a leading name in industrial tooling solutions based in Iwaki, Japan, has recently expanded its TungSpeed-Mill series to include small-diameter, extra close pitch cutters. These innovations cater specifically to industries demanding high-precision milling operations. With bore-type cutters available in ø40 (z=8), ø50 (z=10), and ø63 (z=14) configurations, these tools promise enhanced machining efficiency through their unique designs. Furthermore, the introduction of lightweight steel bodies for ø100 and ø125 models ensures compatibility with smaller machines like BT30, making them versatile across various applications.
Bio Data & Personal Information | Career & Professional Information |
---|---|
Name: Satoshi Kinoshita | Position: President, Tungaloy Corporation |
Date of Birth: Confidential | Industry: Industrial Tooling Solutions |
Place of Origin: Iwaki City, Fukushima Prefecture | Years of Experience: Over 25 years |
For more information, visit the official website: Tungaloy Corporation |
The concept of pitch in milling refers to the distance between cutting edges on a tool. Depending on the application, three primary types exist—coarse, close, and extra-close pitches. Coarse pitches are typically used for roughing operations where material removal rates are prioritized over surface finish. On the other hand, fine or close pitches excel in finishing applications where maintaining dimensional accuracy and achieving superior surface finishes are critical. Extra-close pitches represent the pinnacle of this technology, designed to maximize both feed rates and cutting efficiency while minimizing vibration during operation.
In sports, particularly baseball, the term pitch takes on another dimension entirely. For instance, Yankees starters employ an array of pitches tailored to exploit specific weaknesses in opposing batters. Among these, the cutter—a hybrid between a fastball and a slider—has gained prominence due to its lateral movement away from the pitcher's dominant hand side. CC Sabathia famously utilized his cutter-slider combination effectively throughout his career, leveraging subtle variations to keep hitters guessing.
Similarly, within gaming communities such as MLB 9 Innings or MLB 9 Innings 23, players often debate which pitches reign supreme. While some swear by the two-seam fastball for inducing ground balls, others advocate for the devastating splitter or curveball to induce swings and misses. Each pitch type possesses distinct characteristics affecting how it behaves upon release and interacts with atmospheric conditions, further complicating strategies employed by pitchers at all levels.
At higher altitudes, traditional pitching dynamics undergo significant changes. Studies conducted in environments similar to those experienced in Denver's Coors Field reveal that sinkers maintain their effectiveness despite reduced air density. However, four-seam fastballs lose their characteristic rise, altering the balance between pitch types in starting rotations. To counteract these effects, modern pitchers increasingly incorporate cutters into their arsenals, capitalizing on their ability to generate late-breaking action without sacrificing velocity.
From an engineering perspective, understanding the interplay between different pitches becomes essential when designing advanced milling cutters. Just as a batter must anticipate whether a pitch will tail inward or fade outward, machinists rely on precise calculations regarding tooth spacing and geometry to ensure optimal performance under varying load conditions. By adopting principles analogous to those observed in athletic competition, manufacturers continue pushing boundaries toward greater efficiencies and capabilities.
Considerations around pitch selection extend beyond mere numerical values; they encompass broader implications tied to operational requirements. Fine pitch cutters, for example, prove indispensable when working with severely interrupted surfaces like manifold blocks. Their design allows for smoother transitions across irregular contours, reducing chatter marks and extending tool life. Meanwhile, coarse pitch alternatives remain irreplaceable in heavy-duty applications involving substantial stock removal, where durability outweighs aesthetic considerations.
As industries evolve, so too does the demand for specialized tools capable of addressing emerging challenges. Whether refining techniques in professional athletics or advancing technologies within manufacturing sectors, the underlying principle remains consistent: adaptability drives success. By embracing innovative approaches to cutter pitch optimization, organizations position themselves favorably amidst ever-changing market landscapes.
In summary, the significance of choosing appropriate cutter pitches cannot be overstated. From enhancing productivity in industrial settings to refining strategies in sporting arenas, thoughtful consideration of this parameter yields tangible benefits across disciplines. As demonstrated by recent developments spearheaded by entities like Tungaloy Corporation, staying informed about advancements in tool design empowers professionals to achieve superior results consistently.


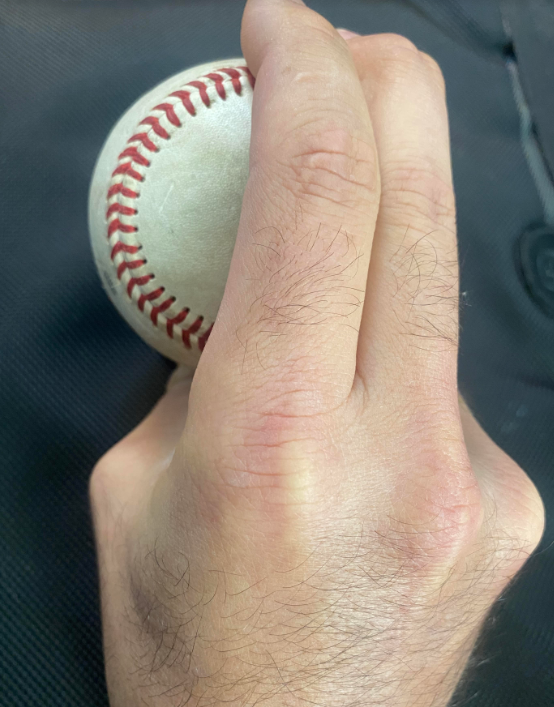
